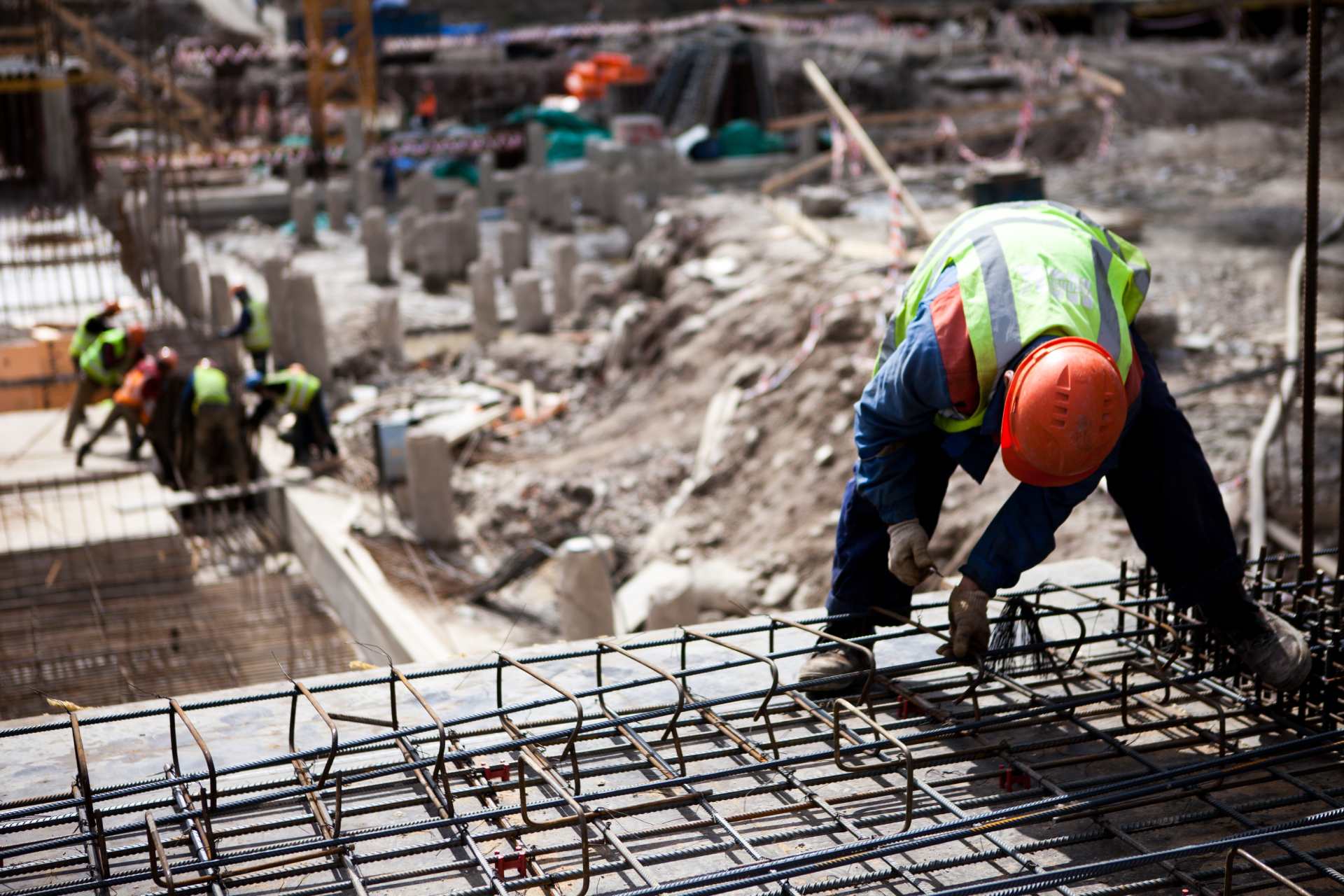
Insulating Concrete Formwork
Insulating Concrete Formwork (ICF)
WHAT ARE ICF’S?
Insulating concrete formwork (ICF), also known as permanently insulated formwork (PIF), is an insulated in-situ concrete system of building that is very quick to construct and offers significantly higher levels of performance than that available from slower, more traditional approaches to building, from the time of ordering a timber frame to arrival on site, we would have the ICF complete, and because in most cases, scaffolding is not needed all ICF walls and floors can be done from the inside, other trades can start much earlier on.
ICF is based on hollow lightweight block components that lock together without intermediate bedding materials, such as mortar, to provide a formwork system into which concrete is poured. The block is formed of sheets of insulation materials, normally expanded polystyrene tied together with plastic or steel ties.
Fresh concrete is poured into the forms built up to 3-metre-high as a complete wall. Once the concrete wall is set, it becomes a high-strength concrete frame structure with the formwork remains in place as thermal insulation, providing u-values ranging from the standard 0.30 w/m²k as required by the current Building Regulations down to 0.11 w/m²k – ideal for zero energy buildings Star Level 6 in the Code for Sustainable Homes. The building process is quick, tidy, and precise, with lower equipment requirements than alternative methods.
Design Flexibility
Allows the specifier to create beautiful, artistic, functional structures with curves, arches, complicated, intricate patterns, and varying angles if needed. Building design is only limited by one’s imagination and, of course, UK planners and local authority approvals.
Variety of Finishes
Unlimited choices of finishes both externally and internally. Externally, renders brick slips, replica stone, stone, brick, tile hanging, sidings wood or vinyl, and internally, plasters or plasterboard, either dot & dabbed or screw fixed.
Compatible to Other Building Systems
the ability to use a range of roofing, flooring, utilities, and opening systems allows the designer total freedom to choose their preferred supporting non-structural building components. Most ICF systems have compatible flooring systems which can be poured at the same time as the supporting walls, but they also all have timber systems where joist hangers penetrate the ICF walls before being concreted in.
Higher Building Performance Standards
Insulated concrete formwork outperforms the current Building Regulations and is eminently suitable for residential construction to Eco-homes with Very Good and Excellent criteria. It is also easily able to meet the requirements of the Code for Sustainable Homes Star Level 3 and, in conjunction with other sustainability supplements …ground source heat pumps, heat exchangers, wind turbines, photovoltaics, etc., can provide solutions up to Code Star Level 6 – Carbon Neutral.
A Modern Method of Construction (MMC)
Insulated concrete formwork (ICF) is a very efficient MMC and will be able to meet the new Code for Sustainable Homes and building regulations requirements which came into force in stages in 2007,2012 & 2016. All new homes to be built after 2016 are to be Code Level 6.
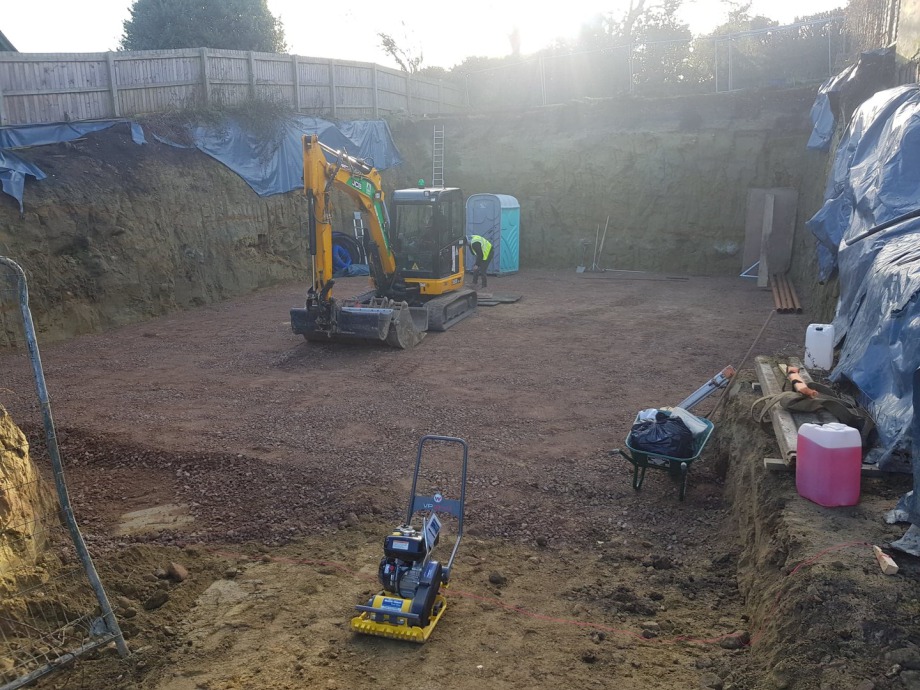
The Developer and ICF
For the Builder Fast Track Construction – Speed of build is one of the unique selling points for considering an ICF solution. It is far faster to build with than Traditional brick & block or frame structure because it takes six to eight weeks from the time you place the order to the time the frame reaches the site, during which an ICF structure could have been completed. Forms are available within three weeks, and the concrete within 48 hours.
Less Down Time – Material availability is on short lead times. The structure can be built in most weather conditions, including rain and frost.
Immediate Follow-On Trades – Insulated Concrete Formwork systems allow the watertight building shell to be erected in days. The follow-on trades can therefore enter the building and start putting utilities and finishes into place much more quickly than traditional building methods.
Simple Service Installation – A great benefit of using an ICF system is the ability to put the conduit, cabling, ducting, etc., for the services you require within the wall space of the empty forms prior to pouring the concrete; this saves time and makes for a very efficient way of construction. This can be supplemented by chasing within the inner wall of polystyrene after the concrete wall has been poured and cured.
Simple Service Installation – A great benefit of using an ICF system is the ability to put the conduit, cabling, ducting, etc., for the services you require within the wall space of the empty forms prior to pouring the concrete; this saves time and makes for a very efficient way of construction. This can be supplemented by chasing within the inner wall of polystyrene after the concrete wall has been poured and cured.
Less Heavy Plant and Equipment – Heavy plant and equipment that you would normally find on the average building site when using traditional building methods is not required with ICF’s. This is due to the lightweight forms and the speed of the modular build.
Good House Keeping – Using Insulated Concrete Formwork makes it very easy to keep the building site tidy and clean, as the forms are easy to stack and waste is kept at a minimum.
Improved Site Safety – This is achieved by the fact that ICF’s are light and easy to handle, so less chance of injury. The workplace is easy to keep tidy, thereby cutting down the possibility of trips, falls, etc., and because the need for plant and other equipment is minimal, chances of accidents are also minimised.
Cost Savings – When all the factors and benefits are taken into consideration, Insulated Concrete Formwork becomes extremely competitive compared to both traditional building methods and lightweight framing. Site examples have proved savings of between 25% to 30% in cost compared to traditional build and lightweight framing if a render is an external wall covering and a further 25% to 30% saving in build time against traditional where materials are on similar lead times. A similar timescale advantage accrues versus lightweight systems if the time starts from the date of frame order.
The Occupier and ICF
Low Running Costs – This is achieved when insulated Concrete Forms are used to build the structure as they offer low ‘U’ Values from 0.3W/m2degk down to 0.11W/m2degk, and they perform to their ‘theoretical calculated design performance’ unlike most materials where a lower U value simply means an improvement on previous. Because dense concrete is the structural core and the layer of insulation is much thicker on the outer leaf (in the lowest U value requirements), “thermal mass” benefits are obtained, which means that the building is warm inside when it is cold outdoors in winter and vice versa in summer. This means you can turn your heating on later in the year and switch it off earlier. Because there is better retention of heat within the building, you can use a small boiler than you would have to had the structure been built out of lightweight materials and in some cases – Passiv Haus Design, a boiler will not be required at all.
As summers in the UK get increasingly warm, air-conditioning will increase, but the thermal mass will minimise the need for air-conditioning, offering further savings against lightweight framed structures not yet considered by regulation but coming soon!
Excellent Acoustic Performance – Due to the density and thickness of the concrete cores within the ICF’s, excellent acoustic insulation is provided, well below the current Building Regulations Part E. Currently (November 2007), pre-completion tests are required since no Robust Details are in place for ICF’s, but to date, all tests with all ICF systems have passed the Building Regulation requirement.
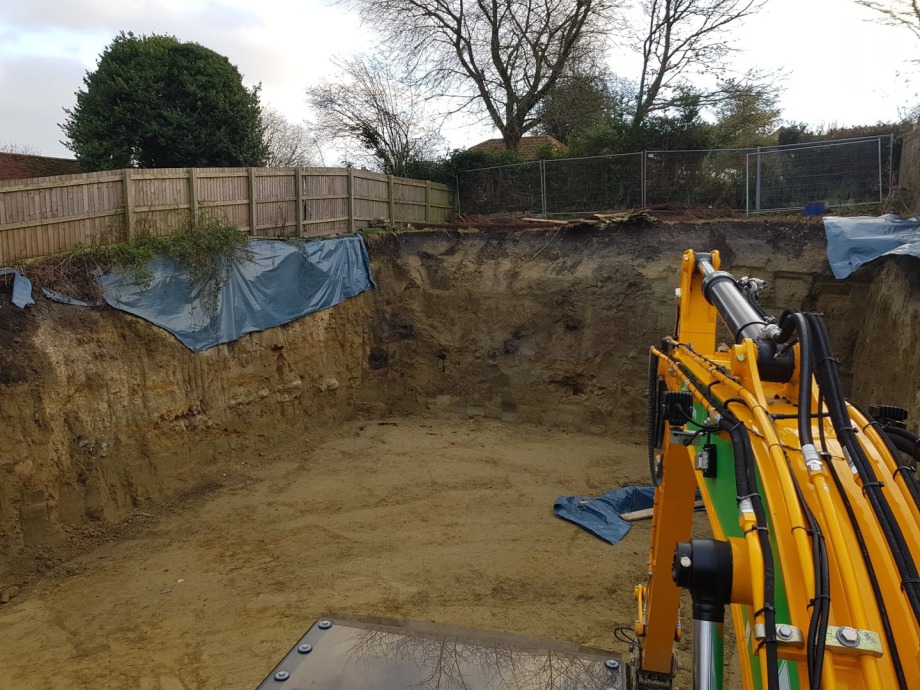
Healthy Indoor Environment – An ICF structure will have minimal air leakage as it is a monolithic structure. North American experience demonstrates that occupants with allergies and chest complaints have minimal difficulties caused by dust, pollen etc., within the property than competitive house-building systems.
Fire Resistance – All Insulated Concrete Formworks provide fire protection more than normal requirements. EPS (expanded polystyrene) is manufactured containing a fire-retardant substance, which means the ICF does not support a flame.
Minimal Flood Damage – Concrete and construction grade EPS are unaffected by water. If ICF buildings are in an area which is subject to possible floods, they will withstand the pressure of water and flood damage will be minimised, especially when compared with building methods. ICF properties exposed to water can be pumped and dried out, leaving the structure integrity unaffected.
ROT and Vermin – ICF structures do not rot and are unaffected by vermin and termites.
Wind Storm & Earthquake – ICF’s developed in North America as basement constructions providing successful protection from heavy storms and high winds, including hurricanes and tornadoes. As market share grew ‘above grade’, there have been numerous examples where ICF houses have stood unaffected whilst lightweight framed structures have been destroyed. Since ICF’s are concrete framed structures, they can be designed to the relevant codes for earthquake zones.
Mortgage, Insurance and Planning Acceptance – ICF structures – concrete framed buildings – are accepted by all reputable companies and organisations, providing they have passed the recognised third-party tests and standards that are needed to obtain building approval. In the UK, ICF’s should have either BRE or BBA certification, and ready-mixed concrete should be supplied from manufacturers offering BSI or QSRMC Quality Assurance schemes.
Easily Adapted for Future Needs – Because concrete frames offer a whole floor space without further load-bearing walls, it is easy to remodel and upgrade floor layouts in the future. The strength of ICF walls allows extra floors to be added subject to authority approval, and it is easy to add and tie in future extensions. The structural walls also will accommodate extra openings in the future, though engineering approval would be needed. If even lower U values are required in the future, extra polystyrene could be fitted externally and reclad.
Minimal Maintenance Required – Under normal circumstances, no maintenance would be required on the ICF walls in the life of the building. The internal and external facades could be subject to minor damage, which be easily repaired or completely stripped and renewed.
The Environment and ICF
ICFs offer Superior Energy Performance and whole-life costs combined with excellent durability.
They can be used for all wall construction types above or below ground, and they are fully recyclable.
They are made from materials which are not scarce, have a chain of custody schemes and are relatively local deliveries to building sites in the UK.
The combination of concrete delivered in exact quantities by a truck mixer and ICFs simply clipped together offers clean, safe building sites with almost zero wastage.
ICF buildings can last for centuries, and their robustness has been recognised by the American Armed Forces, who have used them to build recent bases in the Middle East following successful blast tests in the USA.
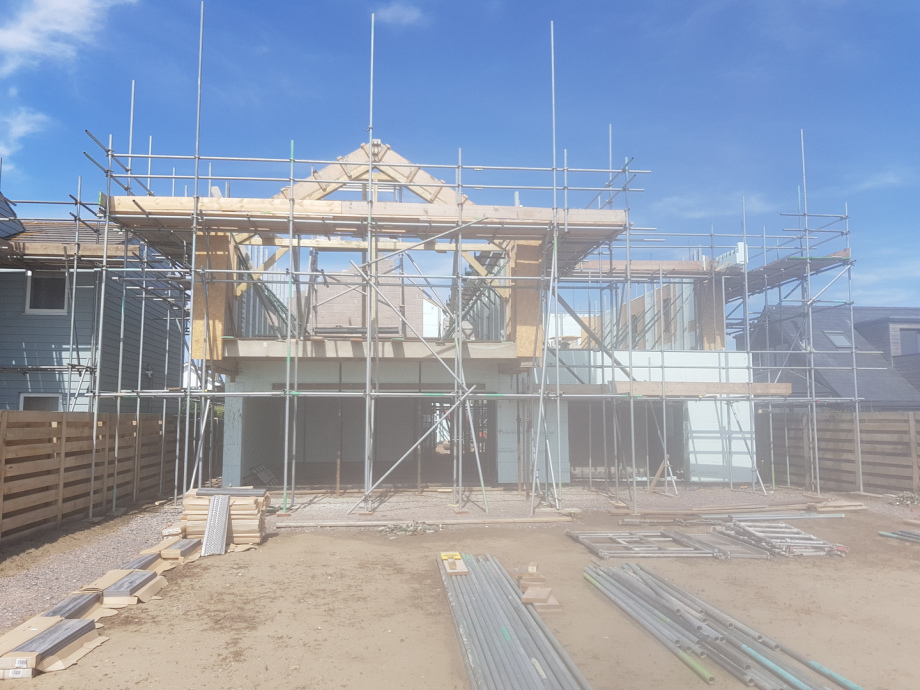